Automated solution for Leading Edge Repair
We have achieved another great milestone in our technology advancement – an automated solution for Leading Edge Repair. We successfully conducted the first LE repair on-site using the Aerones robotic technology. Here is a video of how we repair the Leading Edge in less than 2 hour.
The automated LE repair consists of 5 steps:
No |
Step |
Description |
Time necessary |
1. |
Laser scan |
Scan the blade before the repair and generate a 3D model of the blade in 12 μm (micrometer) precision to assess the blade condition and adjust the tools. |
15min |
2. |
Grinding and sanding |
Remove the damaged/eroded layer to allow for application of a new layer of filler. |
10-20min |
3. |
Decontamination |
Clean up the blade and prepare it for filler application to provide maximal durability of the material applied later. |
10-20min |
4. |
Filler application and profiling |
Apply an exact amount of the filler material on the blade and profile it in a high-precision. |
10-20min |
5. |
Laser scan |
Scan the blade after the repair to validate the result and guarantee the highest quality. |
15min |
– |
Changing the robotic arms |
After each of the steps it is necessary to change the robotic arms. Each of the robotic arms perform different task |
5min x 4 |
– |
Total time |
Time necessary to perform the whole process for one blade |
1.5h – 2h |
Besides LE Repair, the Aerones robotic blade care systems can perform:
- Lightning Protection System (LPS) test (video);
- Detailed visual inspections and data analysis (video);
- Leading-edge protection and ice-phobic coating application (video);
- 3D scanning of the wind turbine blades – to assess energy production efficiency (video);
- Drainage hole cleaning (video);
- Blade cleaning (video).
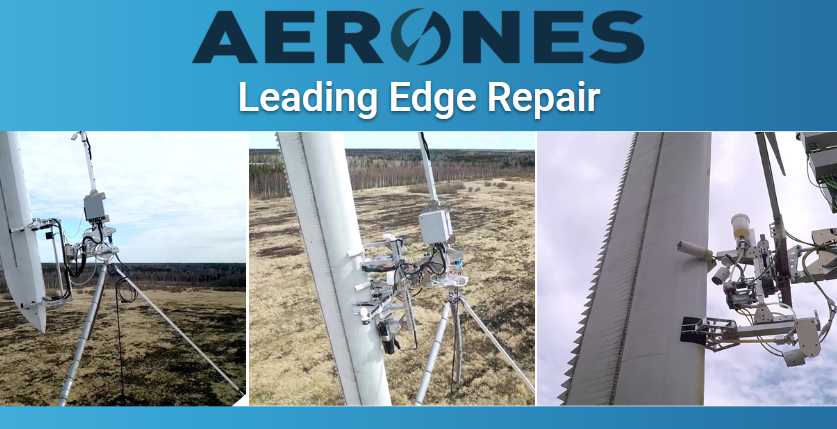